Solar Panel Defects
|
NY TIMES ARTICLE |
|
LOS ANGELES — The solar panels covering a vast warehouse roof in the sun-soaked Inland Empire region east of Los Angeles were only two years into their expected 25-year life span when they began to fail.
Coatings that protect the panels disintegrated while other defects caused two fires that took the system offline for two years, costing hundreds of thousands of dollars in lost revenues.
It was not an isolated incident. Worldwide, testing labs, developers, financiers and insurers are reporting similar problems and say the $77 billion solar industry is facing a quality crisis just as solar panels are on the verge of widespread adoption.
No one is sure how pervasive the problem is. There are no industrywide figures about defective solar panels. And when defects are discovered, confidentiality agreements often keep the manufacturer’s identity secret, making accountability in the industry all the more difficult.
|
|
But at stake are billions of dollars that have financed solar installations, from desert power plants to suburban rooftops, on the premise that solar panels will more than pay for themselves over a quarter century.
The quality concerns have emerged just after a surge in solar construction. In the United States, the Solar Energy Industries Association said that solar panel generating capacity exploded from 83 megawatts in 2003 to 7,266 megawatts in 2012, enough to power more than 1.2 million homes. Nearly half that capacity was installed in 2012 alone, meaning any significant problems may not become apparent for years.
|
|
“We need to face up to the fact that corners are being cut,” said Conrad Burke, general manager for DuPont’s billion-dollar photovoltaic division, which supplies materials to solar manufacturers.
The solar developer Dissigno has had significant solar panel failures at several of its projects, according to Dave Williams, chief executive of the San Francisco-based company.
“I don’t want to be alarmist, but I think quality poses a long-term threat,” he said. “The quality across the board is harder to put your finger on now as materials in modules are changing every day and manufacturers are reluctant to share that information.”
|
|
Most of the concerns over quality center on China, home to the majority of the world’s solar panel manufacturing capacity.
After incurring billions of dollars in debt to accelerate production that has sent solar panel prices plunging since 2009, Chinese solar companies are under extreme pressure to cut costs.
Chinese banks in March, for instance, forced Suntech into bankruptcy. Until 2012, the company had been the world’s biggest solar manufacturer.
Executives at companies that inspect Chinese factories on behalf of developers and financiers said that over the last 18 months they have found that even the most reputable companies are substituting cheaper, untested materials. Other brand-name manufacturers, they said, have shut down production lines and subcontracted the assembly of modules to smaller makers.
|
|
“We have inspectors in a lot of factories, and it’s not rare to see some big brands being produced in those smaller workshops where they have no control over quality,” said Thibaut Lemoine, general manager of STS Certified, a French-owned testing service. When STS evaluated 215,000 photovoltaic modules at its Shanghai laboratory in 2011 and 2012, it found the defect rate had jumped from 7.8 percent to 13 percent.
In one case, an entire batch of modules from one brand-name manufacturer listed on the New York Stock Exchange proved defective, Mr. Lemoine said. He declined to identify the manufacturer, citing confidentiality agreements.
“Based on our testing, some manufacturers are absolutely swapping in cheap Chinese materials to save money,” Jenya Meydbray, chief executive of PV Evolution Labs, a Berkeley, Calif., testing service.
|
|
SolarBuyer, a company based in Marlborough, Mass., discovered defect rates of 5.5 percent to 22 percent during audits of 50 Chinese factories over the last 18 months, said Ian Gregory, the company’s senior marketing director.
Some Chinese manufacturers acknowledge that quality has become a problem
“There are a lot of shortcuts being taken, and unfortunately it’s by some of the more reputable companies and there’s also been lot of new companies starting up in recent years without the same standards we’ve had at Suntech,” said Stuart Wenham, the chief technology officer of Suntech, which is based in Jiangsu Province in eastern China.
|
|
When asked about quality standards, Trina Solar, one of the largest Chinese manufacturers, said in an e-mailed response, “For Trina, quality will not be compromised in our cost-reduction efforts.”
The heart of a solar panel is a photovoltaic cell that generates electricity when struck by sunlight. Among the most critical components are a thin film that protects the cell from moisture, and the encapsulant that seals the cell between layers of glass.
Mr. Gregory said repeat inspections of factories found some manufacturers had been constantly switching to cheaper materials, including some whose use-by date had expired.
“If the materials aren’t good or haven’t been thoroughly tested, they won’t stick together and the solar module will eventually fall apart in the field,” he said.
|
|
That’s what happened in 2011 at a year-old Australian solar plant, Mr. Meydbray of PV Evolution said. Testing confirmed that substandard materials were causing the Chinese-made modules’ protective coating to degrade, he said. The power plant operator declined to be identified.
“I think quality is increasingly a concern, but it’s not a major issue yet,” said Rhone Resch, chief executive of the Solar Energy Industries Association, a trade group. “As companies race to cut their costs, some who are on the edge may take short cuts.”
The Energy Department’s National Renewable Energy Laboratory has studied the performance of solar panels up to 2010, according to Sarah Kurtz, a scientist who manages the laboratory’s photovoltaic reliability group.
“The question is whether things are deteriorating rapidly or whether it’s a few isolated companies not doing so well on their quality control,” she said. “I hear a lot of angst, but I haven’t seen a lot of solid information.”
All solar panels degrade and gradually generate less electricity over time. But a review of 30,000 installations in Europe by the German solar monitoring firm Meteocontrol found 80 percent were underperforming. Testing of six manufacturers’ solar panels at two Spanish power plants by Enertis Solar in 2010 found defect rates as high as 34.5 percent.
Enfinity operates solar installations in Europe and the United States. Bob Hopper, Enfinity’s chief development officer, said his company had stopped buying Chinese modules because of quality concerns. “Even a small amount of unforecasted degradation in electricity production can have significant economic impact on us,” he said.
In the Netherlands, René Moerman, chief strategy officer of Solar Insurance and Finance, said claims had risen 15 percent recently. He said an inspection of a solar plant in Britain in March revealed that 12 percent of the newly installed Chinese-made modules had failed. He said confidentiality agreements prevented him from naming the manufacturer.
|
|
|
|
|
|
|
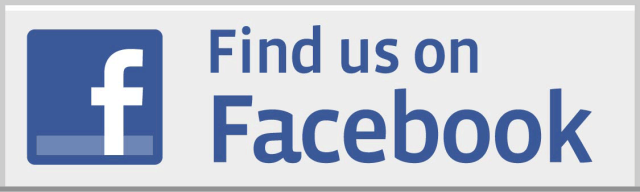 |
|
SO MANY REASONS WHY SOLAR FARMS DO NOT BELONG ON LONG ISLAND ESPECIALLY THE EAST END! |
|
|
STOP THE SOLAR FARMS NOW!
VOTE ALL THOSE POLITICIANS
THAT ALLOW THIS TO HAPPEN OUT!
|
SAVE OUR GREEN SPACES!
FOLLOW THE MONEY TRAIL TO SEE WHICH POLITICIANS AND LAWYERS ARE BENEFITTING THE MOST
|
SAVE OUR WILDLIFE AND WATER BASIN!
THESE PEOPLE SHOULD BE HELD ACCOUNTABLE FOR THIS LAND GRAB
|
|
|
|
|
|
|
|